GET A QUOTE
Specifying the Product
Wood is a natural product. The beauty of veneer is in the natural variations of texture, grain, figure, color and the way it is assembled on a face. The goal of this section is to educate the buyer on the subtle nuances of purchasing a natural wood product.
Here are the recommended steps in specifying or purchasing veneered panels or laminated veneer sheets:
How many sheets does your job require?
Quantity is important because individual flitches are limited in the number of sheets that they can yield. We strongly recommend that you order extra material at the time of your initial order in the event that you need additional material on the job site. By not ordering overage at the time of your original order, you run the risk of extended lead times on replacement material, the inability to match existing material, or the inability to find additional material in the desired species, size, and cut.
What panel core or laminate backer does the job require?
If your job requires anything other than standard cores listed below, please specify such requirements as fire-retardant, moisture resistant or formaldehyde free core. You also need to determine the appropriate thickness of the core.
Panel Core: Laminate Backer:- FormWood® paper-backed veneer provide stability and flexibility while helping to minimize splitting, grain-raise and glue seepage. Sheets are available with 10 mil, 20 mil and 30 mil paper backing.
- NBL® laminates provide the woodworker with superior flexibility and performance when compared to other wood-backed products. NBL's® patented 3-ply construction produces an extremely pliable, moisture-resistant sheet without the black edge associated with phenolic and foil backers. Minor substrate imperfections are "absorbed" and hidden by NBL's® thermo-set joined face and parallel grain, all-wood-backer.
- FormWood 2-Ply veneer has a perpendicular face-to-back construction utilizing a thin acrylic membrane to provide protection against bubbling, glue seepage and telegraphing. The crossband construction allows FormWood 2-Ply veneer to bend on moderate curves in the horizontal or vertical direction.
- DuraBack™ is a unique product designed and engineered as an alternative to traditional laminate backed veneer. This product is very popular in markets where solvent-based adhesive restrictions require woodworkers to use water-based glues. DuraBack™ may also be applied with a solvent-based adhesive. The DuraBack™ sheet's beige backer blends nicely in most applications to maintain the natural beauty of the wood veneer. DuraBack™ offers the stability of laminate, while providing superior flexibility. Also, DuraBack™ accepts pre-finishing prior to lamination and is easily post-formable around curves.
- Utilizing the best quality 3M™ Brand PSA adhesives, our peel & stick veneer provides a permanent bond to any smooth substrate that is dry and free of dust and contaminants. PSA-backed veneer is the perfect choice for cabinet refacing, home craftsmen and professional woodworkers.
What size sheets does your job require?
Width is the measurement across the grain, while length is the measurement with the grain. The first number is always the width and the second is the length.
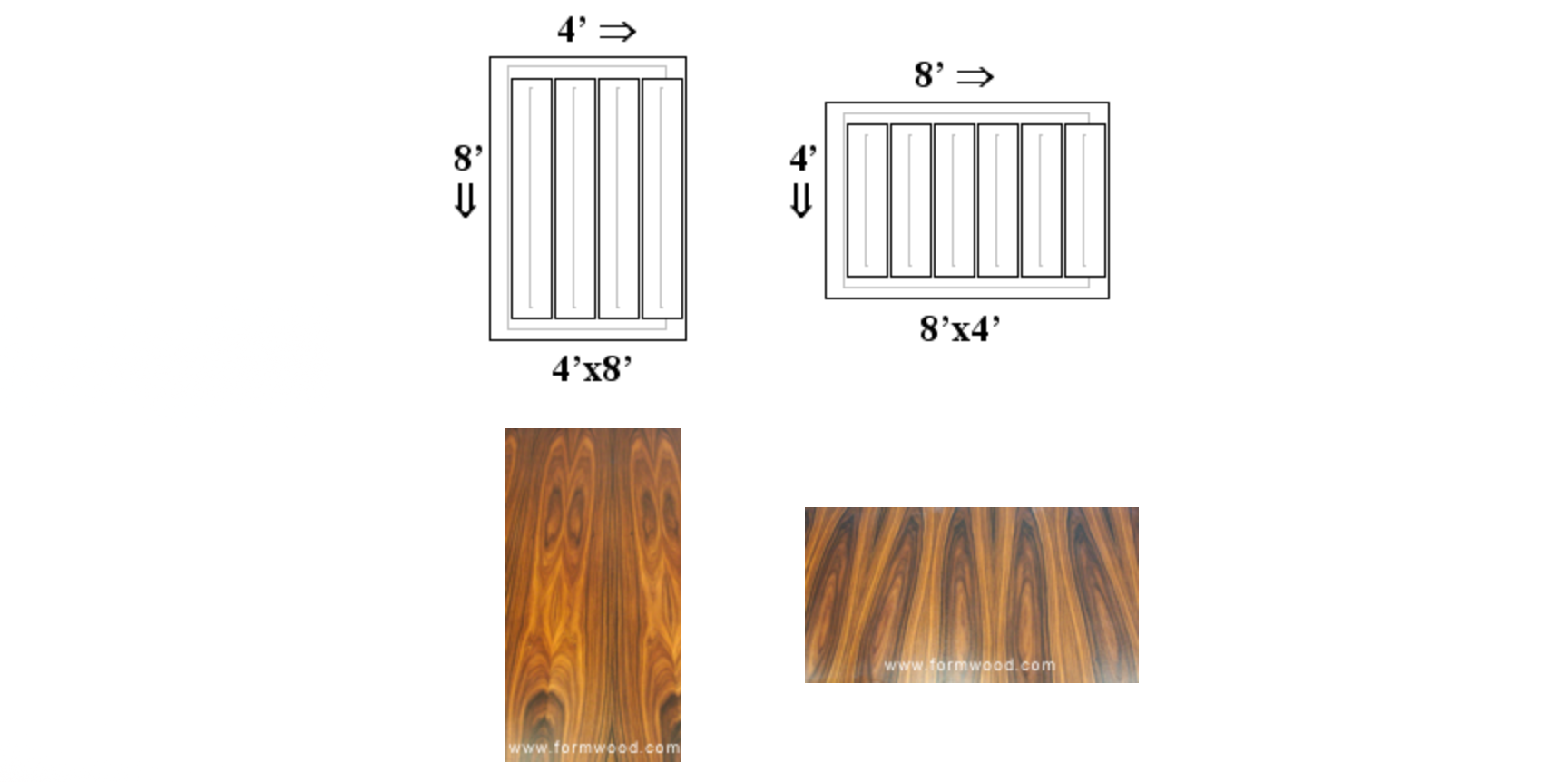
What species best suites your application while also fitting into your budget?
During species selection, consideration should be taken for color, grain, and figure. Also, be sure that the species is available in the quantity and size that you require. FormWood offers over 100 different cuts, species, and veneer. If you have a specific "look" in mind, please request a sample. FormWood offers type samples (represent the species), flitch samples (veneer leaves from a specific log), or digital images. If working with panel core, a balancing backer material will also need to be specified. You may choose the same species that is on the face (A/A), a lower grade of the species that is on the face (A/1 or A/2), a wood backer of any species (A/3), or a balancing backer that is not made of wood (A/4).
Which cut will yield the most complementary look for your job?
The way in which a log is cut in relation to the annual rings determines the appearance of the veneer.
- Flat cut or plain slicing yields a beautiful cathedral effect. The veneer leaves are wider than in quartered or rift slicing. The half log, or flitch, is mounted with the heart side flat against the flitch table of the slicer and the slicing is done parallel to a line through the center of the log.
- Quarter slicing yields a finer figure with a very straight grain. Characteristic flake or ray may appear in red or white oak. The flake size and quantity will vary, even within a single flitch. The quarter log is mounted on the flitch table so that the growth rings of the log strike the knife at approximately right angles, producing a series of stripes. These stripes vary in width from species to species.
- Rift slicing is used only when referring to Red and White Oak as rift cutting can eliminate a flake or ray figure that is often found in this species. The cut slices slightly across the medullary rays.
- Rotary slicing yields wild grain patterns and wide flitches. In some species rotary cuts are available as a whole piece face without any splice lines. This cut follows the log's annual growth rings, providing a generally bold random appearance. Matching of grain or figure from panel to panel is unlikely. The log is mounted centrally in the lathe and turned against a razor sharp blade, like unwinding a roll of paper.
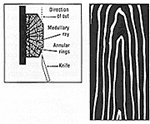
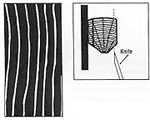
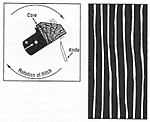
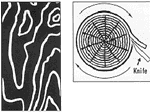
How would you like for the leaves to be arranged on the sheet?
After the log is sliced, the stack of veneer leaves needs to be placed side by side to create veneer faces. The way in which the individual cuts are placed next to each other during fabrication of the veneer face can affect the overall look of the sheet.
- Book Matching is the most commonly used match in the industry. Every other leaf is turned over as it is placed next to its mate. That is, every pair of leaves is opened like a book. When the figure is prominent, a repeating, symmetrical pattern is created. When the veneer is sliced, a distortion of the grain occurs. The knife blade as it hits the wood creates a "loose" side where the cells have been opened up by the blade, and a "tight" side. Because the "tight" and "loose" faces alternate in adjacent pieces of veneer, they may accept stain differently, and this may result in a noticeable color variation called barber poling. This can be minimized, although not always eliminated, with good finishing techniques.
- Slip Matching is often used in quarter cut and rift cut veneer to minimize the barber pole effect. Instead of turning every other leaf, the leaves are merely slipped off the stack, one after another. They are laid side by side just like dealing a deck of cards all face up. The grain figure repeats, but joints won't show mirrored effect.
- In reverse slip matching, the veneer leaves are slipped out from under each other and every other veneer leaf is flipped end to end. This balances the character of the veneer in the panel face.
- End Matching is often used when the area to be paneled is very tall or when the apparent length of short veneer needs to be extended. This is achieved by booking the veneer leaves end to end and then side by side. A sketch or drawing is required for quoting, as there are several different ways to achieve this result.
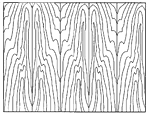
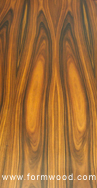
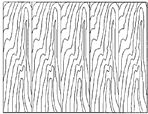
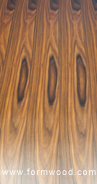
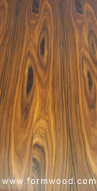
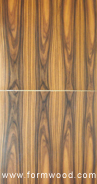
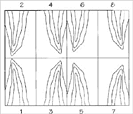
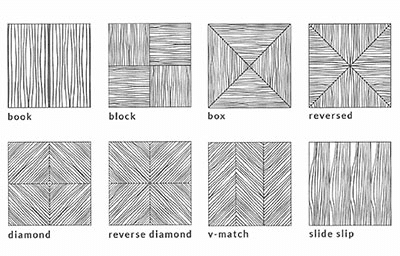
How would you like the single face panel to be fabricated?
- Running Match is the most common method for commodity sheets. Each leaf is clipped to be as wide as practical, which results in each panel having a different number of leaves. The most visible result is the appearance of narrow leaves on the edges of the panels. When a wide leaf is used as the last leaf on the panel, the remainder of the leaf is used to start the next panel. The word running may be mistakenly understood as meaning a running "sequence" of material; however, this term is not related to panel matching.
- Balance matched faces have leaves of approximately the same width all across the face. The two outside leaves will be slightly narrower due to trimming. The face could be made up of an even number of leaves or an odd number of leaves. The number of leaves will change as the faces are fabricated, but because the leaves from the outside of the tree are narrower than the leaves from the center, the number of leaves needed to cover the face of the panel will vary. Due to yield loss in cutting to keep the leaf width the same, this type of matching is more expensive than running match.
- Center Balance Match is similar to balance match in that the leaves are still about the same width across the face, with the outside leaves just a little smaller due to final trimming. The difference is that there will always be an even number of leaves on the face. Each panel will have a center line, with an equal number of leaves to the left and right. Remember that the actual number of leaves on a face will change, just as in balance match, as we move through the flitch. Due to yield loss in cutting to keep the leaf width the same and an even number of components, this type of matching is more expensive than balanced match.
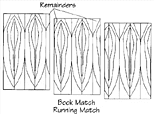
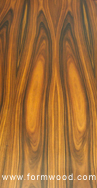
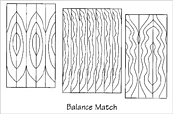
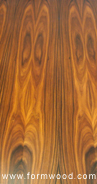
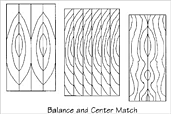
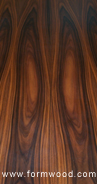
How do you want the panels to be fabricated in relation to each other?
- Flitch matching refers to a set of veneer sheets that have been produced from the same log. In some cases this results in a similarity in color. This option is often more affordable than sequence matching. If color and grain consistency are necessary, please request sequence matching.
- Sequencing refers to a set of veneer sheets that have been produced in order from the same log. The number of sheets per sequence can be limited by species, cut, grain-orientation and yield.
- Blue-print Matched panels are laid up from a working shop drawing. The drawing shows each panel, its size and grain orientation, and its relationship to every other panel on the project. FormWood must have a drawing in order to quote such a specific type of job.
Do you have any special requirements?
This may include sanding specifications, matching to an existing job, density of figure, and others. It is best that we know all of the parameters of the job at the time of quoting because changes can affect the price, lead time, and availability of material.